The Unparalleled World of Die Casting Factories
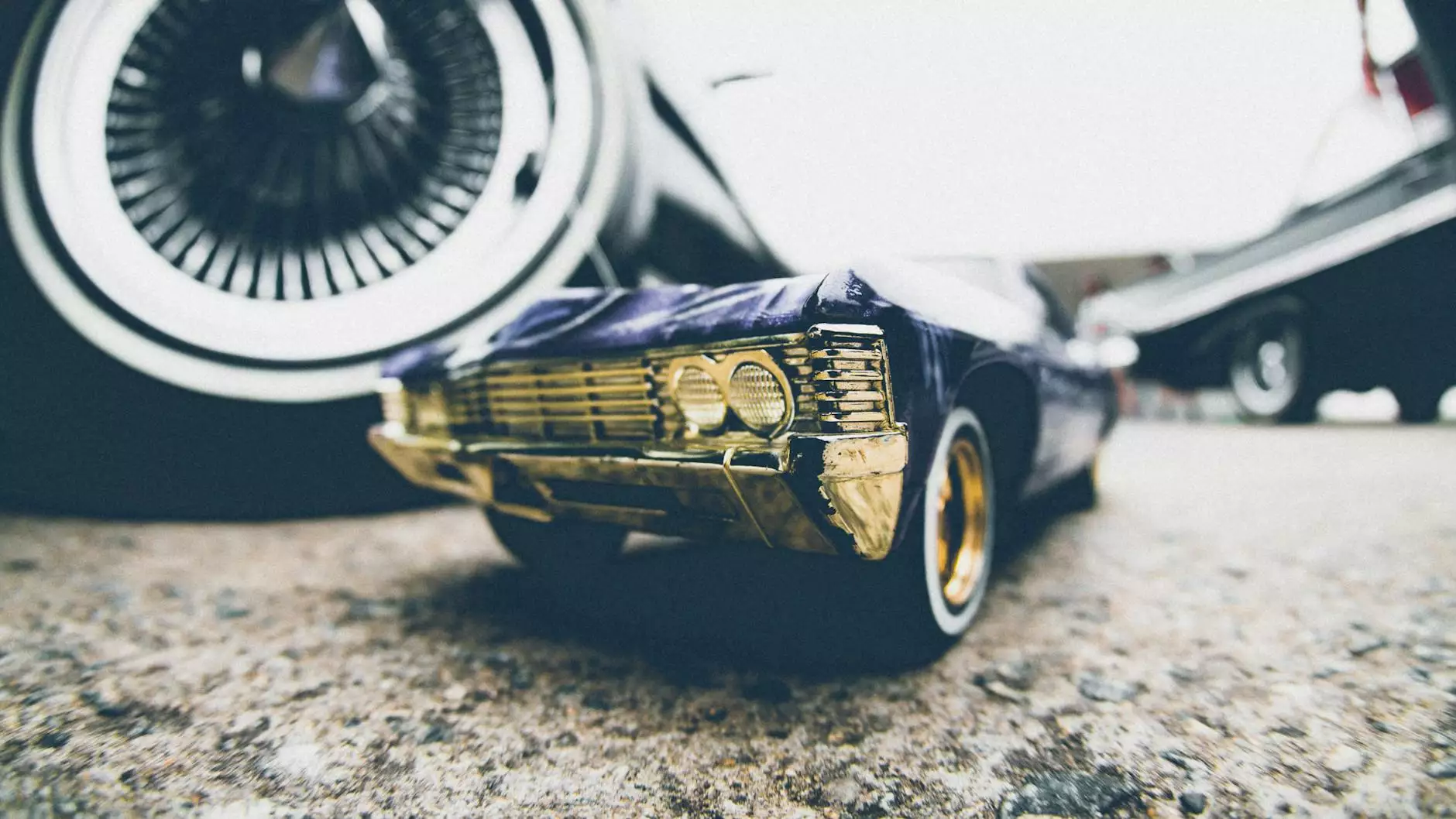
Die casting factories represent a pinnacle of modern manufacturing, specializing in the production of metal components through a highly efficient and precise method. This article delves deeply into the intricacies of die casting, providing a thorough understanding of its processes, advantages, challenges, and its pivotal role in various industries.
What is Die Casting?
Die casting is a metal casting process characterized by forcing molten metal under high pressure into a mold cavity. The result is a meticulously shaped component that boasts excellent surface finish and dimensional accuracy. This method is especially popular for producing complex shapes that would be otherwise difficult to manufacture using traditional methods.
The Process of Die Casting
The die casting process comprises several crucial steps that ensure the creation of high-quality metal parts. Let’s break down these steps for better comprehension:
- Melting the Metal: The desired metal alloy is melted in a furnace, achieving the right temperature for casting.
- Injecting the Metal: The molten metal is then injected into a mold under high pressure, usually ranging from 1,000 to 30,000 psi.
- Cooling: Once the metal fills the mold, it is allowed to cool and solidify, taking on the exact shape of the mold cavity.
- Extracting the Part: After cooling, the dies are opened, and the final casting is ejected.
- Finishing Touches: The casting may undergo additional processes such as trimming, machining, or surface finishing to meet specific requirements.
The Advantages of Using Die Casting
Die casting is known for numerous benefits that make it a favored choice in manufacturing. Some of these advantages include:
- High Precision: Die casting offers exceptional accuracy, enabling the production of components that fit perfectly with minimal post-processing.
- Complex Shapes: It allows for intricate designs that would be challenging to achieve with other fabrication methods.
- Rapid Production: The process is highly efficient, facilitating high-volume production within short timeframes.
- Cost-Effectiveness: While initial setup costs can be high, the overall production cost tends to drop significantly with increased volume.
- Durability: The cast components are known for their strength and durability, making them ideal for a wide range of applications.
Applications of Die Casting
Due to its versatility, die casting finds applications across various industries:
Automotive Industry
In the automotive sector, die casting is used to manufacture lightweight yet strong components such as engine blocks, transmission cases, and wheels.
Electronics
The production of high-precision parts for electronic devices, including housings and connectors, is another significant application of die casting.
Consumer Goods
Many consumer products utilize die cast components, from power tools to kitchen appliances, enhancing their performance and aesthetics.
Challenges Faced by Die Casting Factories
While die casting presents numerous advantages, several challenges must be addressed:
- High Initial Costs: The setup costs for die casting can be substantial, particularly for complex molds.
- Material Limitations: Die casting primarily works with non-ferrous metals such as aluminum, magnesium, and zinc.
- Quality Control: Ensuring consistent quality can be challenging, requiring rigorous testing and inspection protocols.
Future Trends in Die Casting
The future of die casting factories is promising, driven by technological advancements and changing industry demands:
Automation and Robotics
Integrating robotics into die casting processes enhances efficiency, reduces labor costs, and improves safety in factories.
3D Printing and Rapid Prototyping
Employing 3D printing technologies in mold design allows for quicker prototype development, significantly shortening the time to market.
Environmental Sustainability
As industries move towards sustainability, die casting factories are adopting eco-friendly practices, including waste reduction and utilizing recyclable materials.
Choosing the Right Die Casting Factory
Selecting the right die casting factory plays a crucial role in ensuring the success of your manufacturing project. Here are key factors to consider:
- Experience and Expertise: Choose a factory with a strong track record and specialized knowledge in die casting.
- Quality Assurance: Look for stringent quality control measures and certifications to guarantee product standards.
- Technological Capabilities: A factory equipped with advanced technology will likely produce better outcomes.
- Customer Service: Positive communication and support throughout the project are vital for a successful partnership.
The Role of DeepMould in the Die Casting Industry
As a leader in the metal fabrication space, DeepMould specializes in providing high-quality die casting solutions. Their state-of-the-art factory emphasizes precision, efficiency, and customer satisfaction. Here’s what makes DeepMould a top choice:
- Innovative Technology: Leveraging the latest advancements in die casting technology to ensure high-quality outputs.
- Skilled Workforce: A team of experienced professionals dedicated to optimizing production processes and maintaining standards.
- Comprehensive Services: From prototyping to full-scale production, DeepMould offers a spectrum of services tailored to client needs.
Conclusion
Die casting factories are integral to modern manufacturing, providing efficient solutions for high-demand industries. As advancements continue to reshape the landscape, staying informed and choosing the right partners will be pivotal to harnessing the full potential of die casting. Embrace the future of manufacturing with a strong understanding of die casting processes and the advantages they offer.
Get in Touch with Us!
If you’re looking for a reliable die casting factory or need more information about our services at DeepMould, don’t hesitate to contact us today. Let’s explore how we can meet your manufacturing needs together!