Understanding Plastic Injection Molding Manufacturing: A Comprehensive Guide
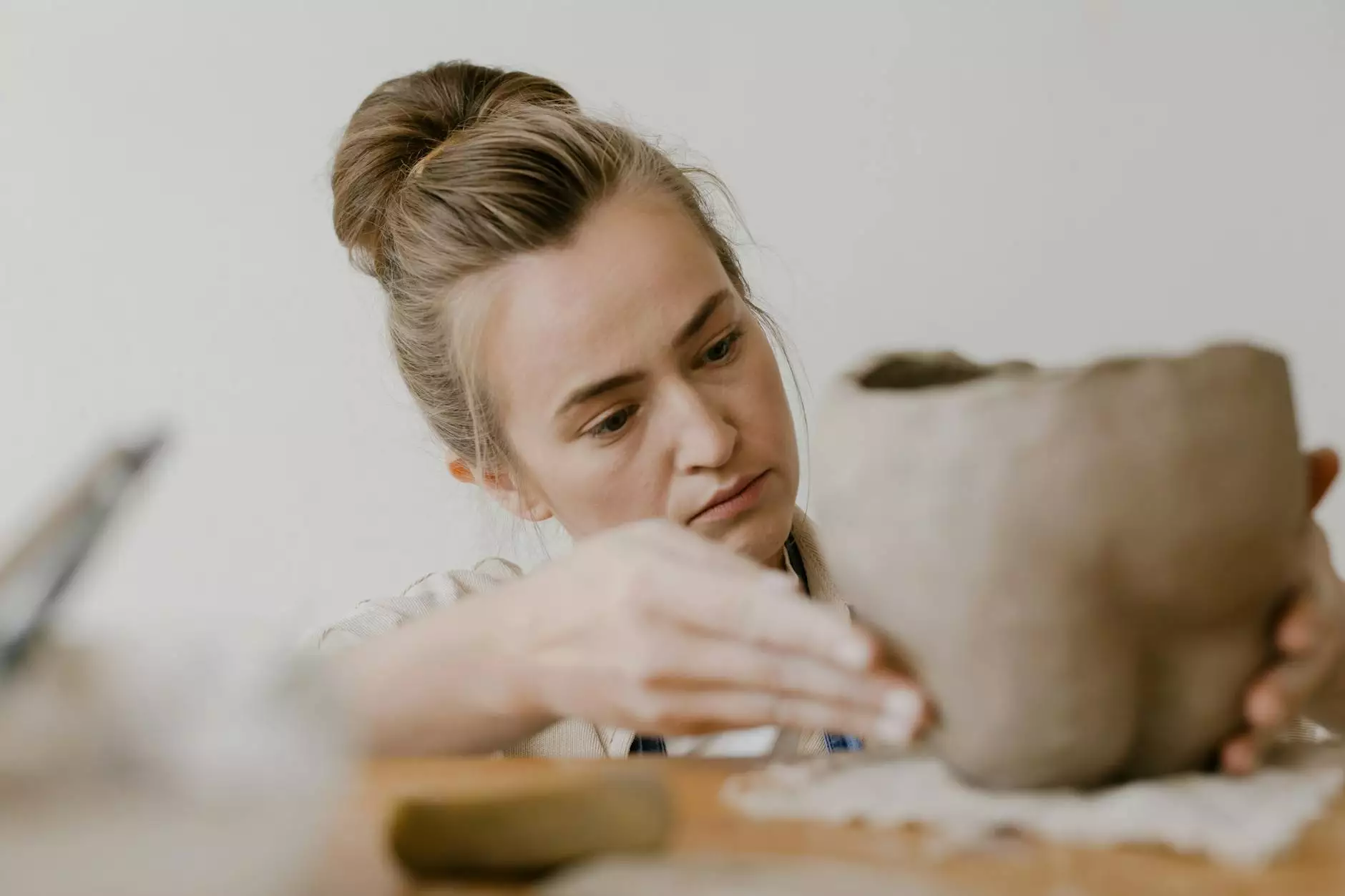
Plastic injection molding manufacturing is a revolutionary process that has transformed the way we produce plastic parts and components across various industries. This article delves deep into the intricacies of this manufacturing technique, exploring its benefits, applications, and the reasons it has become a staple in modern production environments.
What is Plastic Injection Molding?
At its core, plastic injection molding is a manufacturing process used to create parts by injecting molten plastic into a mold. The process begins with the selection of raw plastic, which is then melted down and forced into a mold cavity under high pressure. Once cooled and solidified, the mold is opened, and the finished part is ejected. This method is known for its ability to produce complex shapes with high precision and repeatability.
The Components of Plastic Injection Molding
The plastic injection molding manufacturing process involves several key components:
- Injection Mold: The custom-designed tool used to shape the plastic during the injection process.
- Injection Machine: A machine that melts and injects the plastic material into the mold.
- Plastic Material: Commonly used materials include thermoplastics such as ABS, polycarbonate, and polystyrene.
- Cooling System: A system integrated into the mold that helps to cool and solidify the plastic quickly.
- Ejector System: Mechanism that ejects the finished part from the mold once it has cooled.
The Advantages of Plastic Injection Molding
There are numerous advantages to choosing plastic injection molding manufacturing for your production needs:
- High Efficiency: Once the mold is designed and set up, the production process can achieve high cycle times, allowing for mass production of plastic parts.
- Precision and Repeatability: This method produces components with extreme accuracy, ensuring that each part meets specifications every time.
- Design Flexibility: Complex designs and geometries can be achieved, which are often difficult or impossible with other manufacturing methods.
- Minimal Waste: The process is efficient, resulting in very little scrap material, making it environmentally friendly.
- Cost-Effective for Large Runs: While initial setup costs can be high, the cost per part decreases significantly with large production runs.
Applications of Plastic Injection Molding
The versatility of plastic injection molding manufacturing leads to numerous applications across various sectors:
1. Automotive Industry
The automotive sector heavily relies on injection molding for producing dashboard components, bumpers, and interior trims. The ability to produce lightweight yet durable components is critical for modern vehicle design.
2. Consumer Products
Everyday items, such as plastic containers, toys, and household appliances, are often produced using this efficient method. The design flexibility allows for innovative product solutions that cater to consumer needs.
3. Medical Devices
In the medical field, injection molding is used to manufacture various devices, including syringes, implants, and components for diagnostics. Special biocompatible materials can be used ensuring safety and compliance with stringent regulations.
4. Electronics
Many electronic devices rely on injection-molded parts for enclosures, buttons, and connectors. The process allows for precision manufacturing essential for electronic applications.
5. Industrial Applications
Industrial equipment often includes parts made via injection molding due to their durability and ability to withstand harsh working conditions.
The Process of Plastic Injection Molding Manufacturing
The plastic injection molding manufacturing process can be broken down into several distinct steps:
- Material Selection: Choosing the right type of plastic based on the desired properties of the final product.
- Injection Mold Design: Creating a mold that can accommodate the desired shapes while factoring in material flow and cooling.
- Molding Process Setup: Setting up the injection molding machine with the molds and pre-heating where necessary.
- Injection: The plastic is heated until it melts and is then injected into the mold at high pressure.
- Cooling: The injected plastic needs time to cool and solidify in the mold, which is facilitated by a cooling system.
- Ejection: Once cooled, the part is ejected from the mold, often using an automated ejection system.
- Finishing Processes: Additional processes such as trimming, painting, or assembly may follow the initial molding.
Challenges in Plastic Injection Molding Manufacturing
While plastic injection molding offers significant advantages, there are challenges that manufacturers must navigate:
- High Initial Costs: The investment in molds and machinery can be substantial, which might be a barrier for small productions.
- Long Lead Times for New Designs: Developing new molds can take time, prolonging the product development cycle.
- Material Limitations: Not all types of plastics are suitable for injection molding, which can limit material selection.
- Environmental Concerns: While the manufacturing process is waste-efficient, the end-of-life of plastic products poses recycling challenges.
Future Trends in Plastic Injection Molding
The plastic injection molding manufacturing landscape is evolving, with several trends shaping its future:
1. Sustainability Initiatives
As environmental concerns grow, the plastic industry is exploring biodegradable materials and more sustainable practices in the molding process.
2. Advanced Technologies
The integration of technologies such as 3D printing for prototyping molds and smart manufacturing solutions can streamline production and reduce costs.
3. Customization
With advances in technology, more manufacturers are offering customized solutions for niche markets, adapting molds and processes to meet specific client needs.
Conclusion
In summary, plastic injection molding manufacturing stands as a pillar of modern production, enabling manufacturers to produce intricate and high-quality parts across various industries. With its advantages, such as efficiency, precision, and design flexibility, it will continue to be pivotal in shaping the future of manufacturing. Adapting to challenges and embracing new trends will ensure that this method remains at the forefront of industrial innovation.
For more insights and advanced solutions in plastic injection molding, consider collaborating with industry leaders like DeepMould, where expertise meets innovation to bring your ideas to life.