Unlocking the Potential of Plastic Molding Services
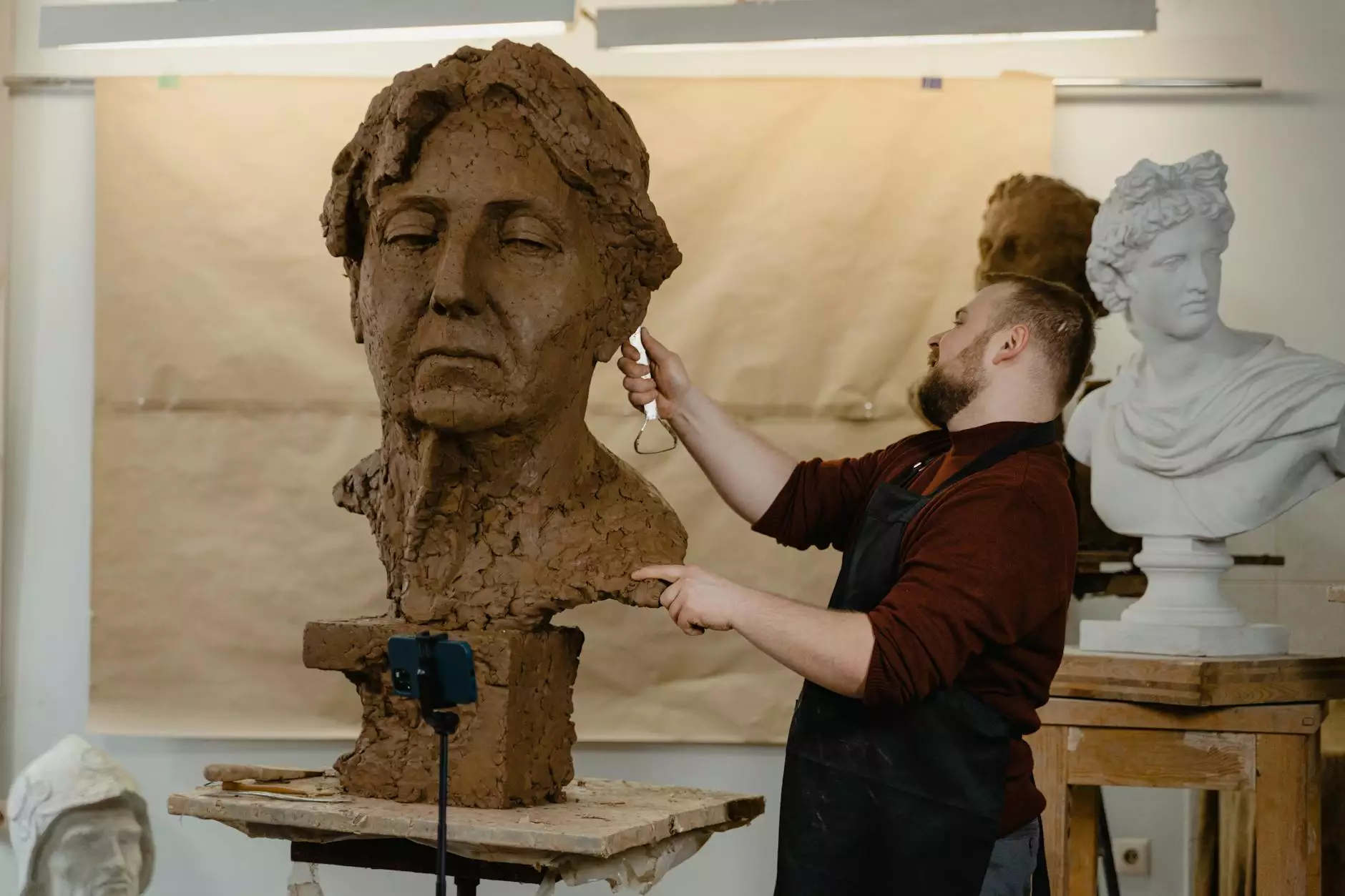
Plastic molding services represent a critical sector in manufacturing, serving various industries with innovative and cost-effective solutions. From creating components for automotive to medical applications, the versatility of plastic molding is unparalleled. At DeepMould.net, we explore how these services can enhance your business operations, driving efficiency and boosting productivity.
What is Plastic Molding?
Plastic molding is a process used to create parts and products by shaping liquid or plastic materials into a desired form. This process involves numerous methods, each tailored to specific applications and material requirements. Here, we'll delve into the major types of plastic molding that are shaping the industry today.
Types of Plastic Molding Processes
- Injection Molding: This is the most prevalent method, where molten plastic is injected into a mold. The result is high-precision, complex parts with minimal waste.
- Blow Molding: Used primarily for hollow items, this process involves inflating a heated plastic tube into a mold to create products like bottles and containers.
- Compression Molding: In this method, plastic is heated and then pressed into a mold, ideal for large components and products with uniform thickness.
- Rotational Molding: This technique is perfect for creating large, hollow objects. The process involves rotating a mold filled with plastic, allowing even distribution and minimal seams.
- Thermoforming: A sheet of plastic is heated and formed over a mold, which is great for creating trays, containers, and panels.
The Advantages of Utilizing Plastic Molding Services
Choosing plastic molding services can transform your production process. Here’s how:
1. Cost-Effectiveness
One of the most significant benefits of plastic molding is its cost-effectiveness. Once the initial design is created, manufacturers can produce large quantities of identical parts at minimal incremental costs. This scalability is crucial for businesses looking to maintain low production costs while meeting market demand.
2. High Precision and Consistency
Plastic molding methods, particularly injection molding, offer unmatched precision. This accuracy means that parts will have tight tolerances and will be consistent across large production runs, ensuring quality control without extensive manual intervention.
3. Design Flexibility
Modern plastic molding allows for complex designs that can include multiple features and integrations into a single component. This flexibility enables companies to innovate and design parts that were previously impossible to manufacture efficiently.
4. Minimal Waste Generation
The efficiency of plastic molding contributes to reduced waste through processes that are designed to utilize almost all of the input materials. This ecological consideration is increasingly important given today's sustainability standards.
5. Wide Range of Materials
Plastic molding services utilize a variety of materials, from thermoplastics to thermosetting polymers. This diversity means that businesses can choose the most suitable material for their specific applications, whether they require flexibility, durability, or resistance to heat and chemicals.
Applications of Plastic Molding in Various Industries
The versatility of plastic molding services allows for applications across many fields, including:
1. Automotive Industry
Automakers leverage plastic molding for components such as dashboards, bumpers, and interior fixtures. The lightweight nature of molded plastics contributes to fuel efficiency while maintaining safety standards.
2. Medical Sector
In the medical field, precision is paramount. Plastic molding creates essential components such as surgical instruments, device casings, and medication packaging that meet stringent regulatory standards.
3. Consumer Goods
From household appliances to toys, plastic molding shapes the everyday items that consumers rely on. The ability to mold complex designs means greater innovation in product development.
4. Electronics Manufacturing
Plastic enclosures for electronic devices are often produced via plastic molding techniques due to the need for lightweight, durable solutions that can house sensitive components while offering insulation.
Choosing the Right Plastic Molding Service Provider
When considering plastic molding services, it’s crucial to select a provider that aligns with your business goals and quality standards.
Key Considerations
- Expertise and Experience: Ensure the provider has proven experience in your industry and understands the unique challenges and requirements.
- Technology and Equipment: A top-tier provider will stay current with the latest molding technologies to enhance production capabilities.
- Quality Assurance: Verify that the company has robust quality control processes to maintain product integrity and meet regulatory compliance.
- Customer Support: Excellent support can streamline communication and problem resolution throughout your project.
- Cost Competitiveness: Compare pricing strategies, ensuring you receive value while determining the long-term benefits of quality workmanship.
The Future of Plastic Molding Services
As we advance into an era dominated by innovation and sustainability, the plastic molding services sector is evolving. Key trends affecting the future of plastic molding include:
1. Sustainable Materials
Increasing environmental awareness has prompted a shift toward using recycled and biodegradable plastics in molding processes. Businesses are re-evaluating their material choices to align with eco-friendly initiatives.
2. Advanced Manufacturing Technologies
The rise of automation and Industry 4.0 principles is transforming plastic molding. Integration with smart technologies allows for real-time monitoring and adjustments, enhancing efficiency and reducing waste.
3. Customization and Rapid Prototyping
With rapid prototyping services available, companies can now create customized products quickly, enabling faster time-to-market for innovative solutions.
4. Improved Supply Chain Management
Global supply chain dynamics are shifting, and businesses are opting for local suppliers for plastic molding services to reduce lead times and improve reliability.
Conclusion
In conclusion, plastic molding services are indispensable to a multitude of industries. The benefits of cost-effectiveness, precision, design flexibility, and minimal waste make this manufacturing method a go-to solution for many companies. With advancements in technology and a growing focus on sustainability, the future of plastic molding is bright. For businesses seeking to enhance their manufacturing capabilities, exploring the options available on DeepMould.net could lead to transformative results.
Your Next Step
Are you ready to explore how plastic molding services can revolutionize your business? Contact us at DeepMould.net to learn more about our tailored solutions and how we can support your manufacturing needs.