The Blades Factory: Mastering Knife Production and Precision
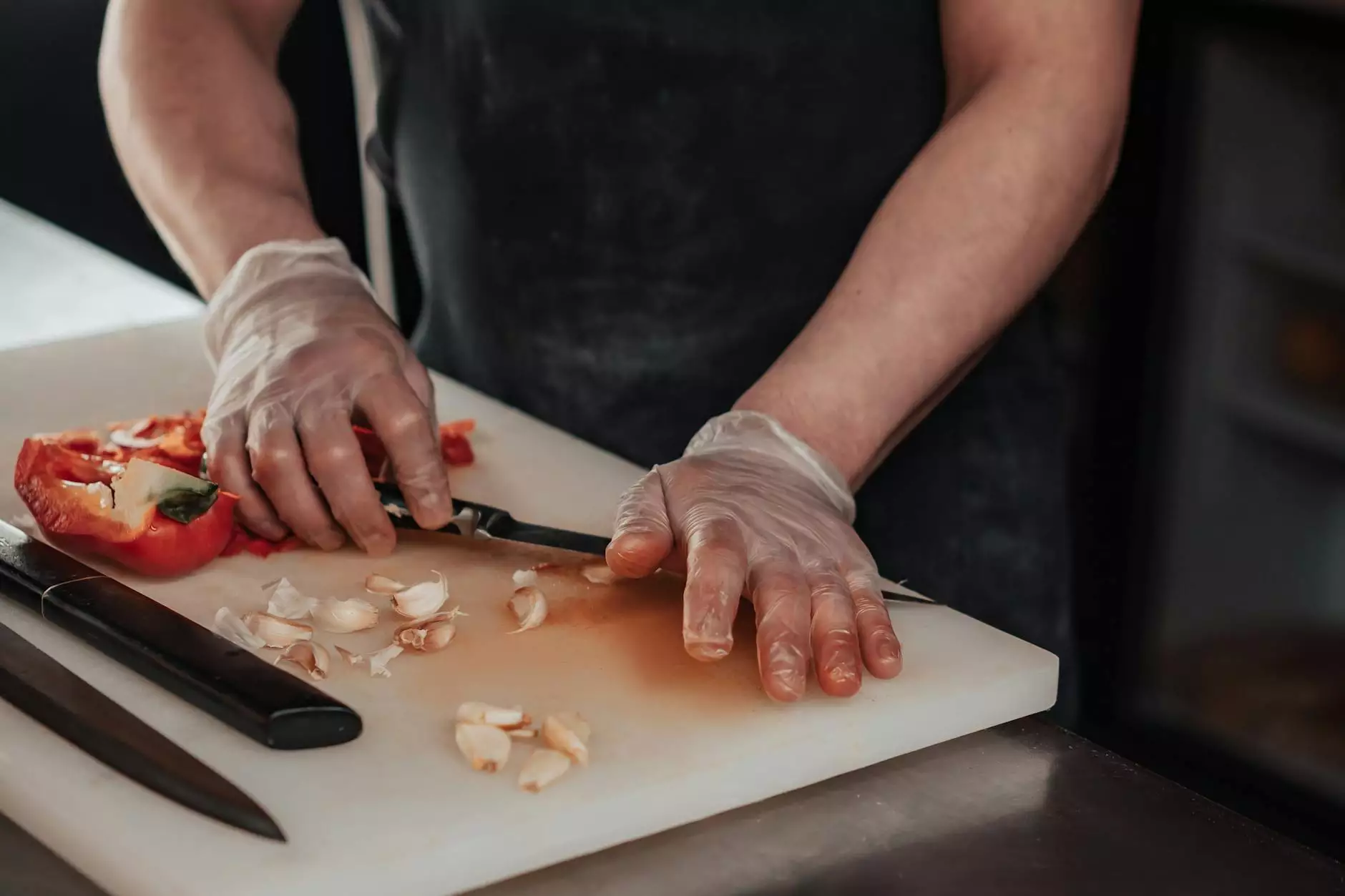
The blades factory plays an essential role in our modern world, producing tools that are vital for various professional services. From culinary chefs wielding the sharpest knives to industrial factory workers utilizing precision cutting tools, the impact of a blades factory cannot be overstated. This article will delve deep into the intricacies of a blades factory, showcasing its pivotal role in the production and sharpening of knives and other cutting instruments.
Understanding the Blades Factory
A blades factory is not merely a production facility; it is a hub of innovation and craftsmanship. These factories are equipped with advanced machinery and skilled artisans who work together to create high-quality blades that meet the demands of various industries.
The Historical Significance of Blades Manufacturing
The art of blade making dates back thousands of years, with early civilizations utilizing rudimentary materials to create edges for tools and weapons. As time progressed, so did the technology and methodology behind blade production:
- Ancient Development: Early blades were crafted from stone and bronze, showcasing the ingenuity of early humans.
- Medieval Advancements: The discovery of iron and steel provided a new paradigm in blade strength and durability.
- Modern Techniques: Advanced metallurgy and precision engineering have revolutionized blade manufacturing, allowing for the production of incredibly sharp and resilient edges.
The Process of Blade Manufacturing
Modern blades factories employ a sophisticated process that incorporates numerous steps to ensure that each blade produced is of the highest quality. Here’s a detailed look at the essential stages involved in blade manufacturing:
1. Material Selection
The journey of a knife begins with the careful selection of materials. High-quality steel is often the primary material, chosen for its durability, edge retention, and ease of sharpening. Other materials, such as ceramic or composite substances, may also be used for specific applications.
2. Forging and Shaping
Once the materials are selected, they undergo forging, a process that involves heating the metal to high temperatures and shaping it through hammering or pressing. This step is crucial for imparting the desired characteristics of strength and flexibility:
- Hot Forging: Involves shaping the metal while it is still hot, promoting better molecular alignment.
- Cold Forging: Allows for precise shaping at room temperature, ideal for detail-oriented knife designs.
3. Heat Treatment
Heat treatment is a critical process that enhances the blade's hardness and toughness. This involves heating the blade to a specific temperature and then rapidly cooling it, a process known as quenching. The blade is then tempered to reduce brittleness while maintaining sharpness.
4. Grinding and Polishing
After heat treatment, the blades are ground to achieve the perfect edge angle and polish to provide a pristine finish. This step is vital, as the sharpness and aesthetic appeal of the blade greatly affect its usability and marketability:
- Surface Grinding: Ensures a smooth finish and uniform thickness across the blade.
- Edge Grinding: Crafting the precise edge angle that defines the blade’s cutting ability.
5. Assembly and Final Inspection
For multi-part knives, assembly is the final step, involving the attachment of handles and other components. Following assembly, a rigorous quality inspection ensures that every blade meets the factory’s high standards.
Importance of Knife Sharpening
Sharpening is a crucial service offered by the blades factory that ensures optimal performance of knives:
Enhancing Performance
Over time, even the best knives lose their edge. Regular sharpening restores the blade’s sharpness which is essential for:
- Precision Cutting: A sharp knife allows for cleaner cuts, enhancing the presentation of culinary dishes.
- Increased Safety: Dull knives are less safe, as they require more force to cut, increasing the risk of slips.
- Extended Lifespan: Careful maintenance through regular sharpening can extend the life of a knife significantly.
Traditional vs. Modern Sharpening Techniques
Knife sharpening techniques have evolved, with traditional methods still holding significant value. Here are some common techniques:
- Whetstones: A popular traditional method offering precision and control.
- Sharpening Steel: Used for honing blades to keep them sharp between proper sharpenings.
- Electric Sharpeners: Providing quick and consistent sharpening for those seeking convenience.
Choosing the Right Blades Factory
When seeking a reliable blades factory, it's crucial to consider several factors that can influence your choice:
Quality Assurance
Look for factories that prioritize quality control throughout their manufacturing process. Ensure they have certifications and a proven track record of producing high-quality blades.
Customization Options
Different users may require unique blades. A good factory should offer customization options to cater to specific needs:
- Custom Shapes and Sizes: Catering to various industries including culinary, industrial, and outdoor.
- Material Selection: Providing options for different blade compositions and finishes.
Customer Service and Support
Choose a factory that offers excellent customer service. This includes:
- Responsive Communication: Quick responses to inquiries and questions.
- After-sales Support: Assistance with maintenance and any issues that arise post-purchase.
The Future of Blade Manufacturing
The future of the blades factory is promising, with advancements in technology paving the way for more efficient and sustainable production methods. Some emerging trends include:
Eco-friendly Manufacturing
As sustainability becomes increasingly important, blades factories are exploring eco-friendly practices, including:
- Recycling Materials: Utilizing recycled metals to reduce environmental impact.
- Reducing Waste: Implementing processes that minimize scrap and waste during production.
Smart Manufacturing
The rise of Industry 4.0 is influencing blades factories, with smart technologies integrating into the manufacturing processes:
- Automation: Robots and automated systems can enhance production efficiency and precision.
- Data Analytics: Leveraging big data can inform better material choices and production schedules.
Conclusion
In summary, the blades factory is a cornerstone of numerous industries, providing essential tools that empower professionals to perform their tasks effectively and safely. By understanding the intricate processes involved in blade production and sharpening, as well as the emerging trends that promise to reshape this industry, we can appreciate the craftsmanship and innovation that goes into making every blade. As the demand for high-quality knives continues to grow, investing in a reputable blades factory becomes paramount for anyone in need of precision cutting tools.