The Essential Guide to Injection Mold Tools
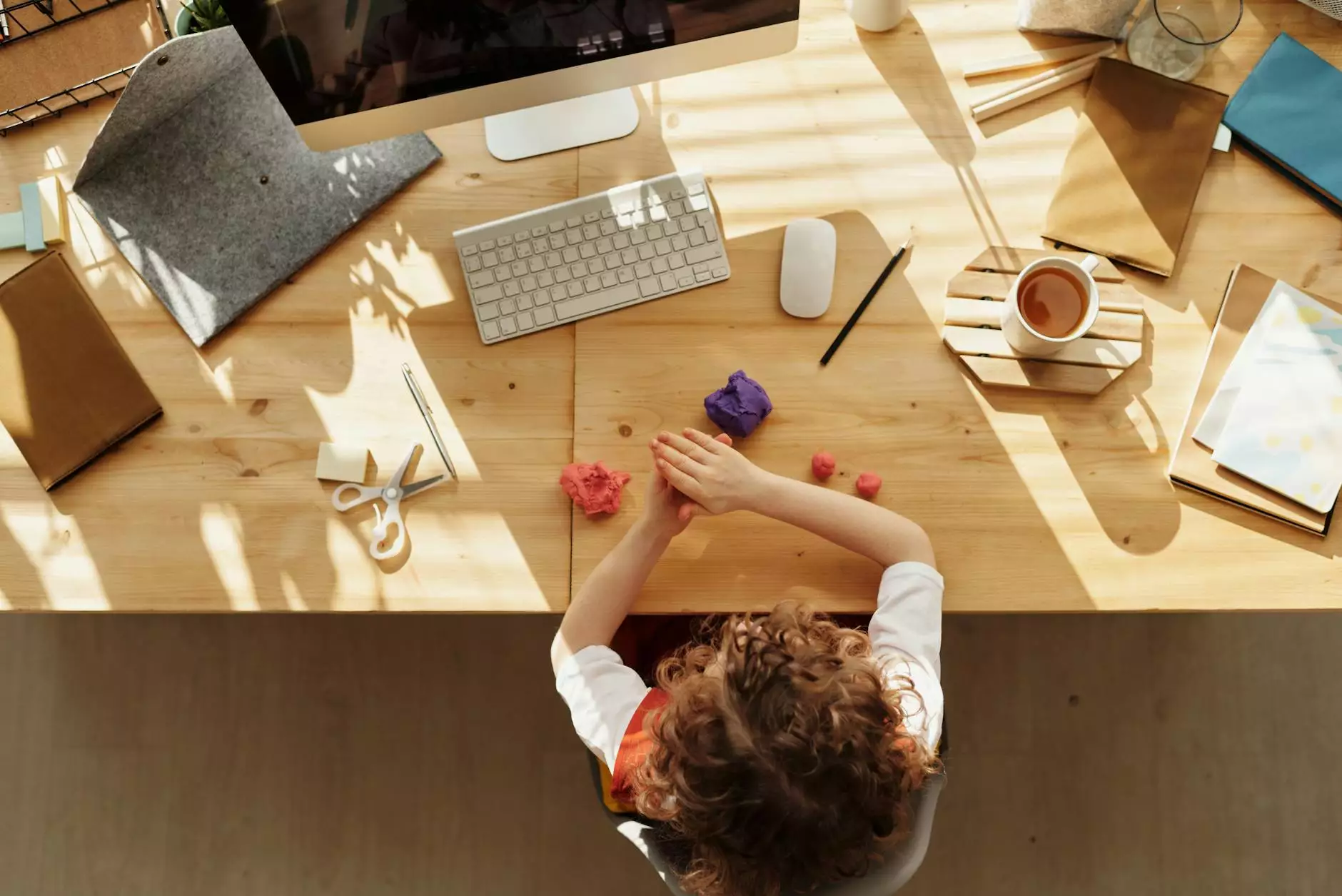
In the modern manufacturing landscape, injection mold tools play a crucial role in producing high-quality plastic components that are integral to numerous industries. From automotive to consumer electronics, the impact of effective molding can be felt in every corner of the production line. This comprehensive guide will delve into the specifics of injection mold tools, exploring their types, benefits, and crucial considerations when selecting the right tools for your manufacturing needs.
Understanding Injection Mold Tools
Injection mold tools are specialized devices designed to create parts by injecting molten material into a mold. These tools are primarily used for producing plastic parts, although they can also be employed for metals in certain applications. The process involves a few key components:
- Molds: The core of the process, molds are custom-designed cavities that determine the shape of the final product.
- Injection Unit: This part of the machine melts the material and injects it into the mold under high pressure.
- Clamping Unit: It holds the mold tightly closed during the injection phase to prevent material leakage.
Types of Injection Mold Tools
There are various types of injection mold tools tailored for different manufacturing needs. Understanding these types can help in selecting the right tool for specific applications.
1. Single Cavity Molds
Single cavity molds are designed to produce one part per cycle. They are simple but effective for low-volume production and prototyping.
2. Multi-Cavity Molds
Multi-cavity molds allow for the production of multiple parts in a single cycle, significantly improving efficiency and reducing production costs in high-volume manufacturing.
3. Family Molds
Family molds contain multiple cavities for different parts, allowing for the simultaneous production of related components, making it ideal for assemblies.
4. Hot Runner Molds
Hot runner molds use a heating system to keep the plastic in a molten state within the runner system, reducing waste and improving cycle time.
5. Cold Runner Molds
In cold runner molds, the plastic cools and hardens in the runner, which can lead to more waste but is often easier to maintain and cheaper to produce.
Advantages of Using Injection Mold Tools
The selection of injection mold tools offers multiple advantages to manufacturers, enhancing both the production process and the quality of the end products.
- High Precision: Injection mold tools allow for the creation of highly accurate and intricate designs, enabling manufacturers to produce components that meet tight tolerances.
- Efficiency: The speed of the injection molding process significantly reduces production time and costs, especially in high-volume runs.
- Material Versatility: A wide range of materials can be used, including thermoplastics, thermosetting plastics, and even metals.
- Reduced Waste: With precise molding capabilities, the amount of excess material is minimized compared to traditional manufacturing processes.
- Scalability: Injection molds can be easily scaled for increased production without compromising quality.
Considerations When Selecting Injection Mold Tools
Selecting the right injection mold tools requires careful consideration of several factors to ensure optimal performance and cost-effectiveness.
1. Material Compatibility
Evaluate the materials you intend to use. Different molds are designed for different types of plastics and metals. Ensure that the chosen mold is compatible with your manufacturing material.
2. Design Complexity
The complexity of the part design plays a critical role in mold selection. Intricate designs may require more advanced tooling, such as hot runner systems or multi-cavity molds.
3. Production Volume
Your production needs will heavily influence your mold choice. High-volume production favors multi-cavity molds, while low-volume runs may benefit from single cavity molds.
4. Lead Time
Consider the lead time for mold production. Customized molds take time to design and manufacture, which can impact your overall production schedule. Select a provider that can meet your timelines.
5. Cost
The upfront cost of molds can be significant, but it’s crucial to evaluate long-term ROI. Investing in high-quality molds can lead to lower production costs over time.
The Role of Metal Fabricators in Injection Molding
Metal fabricators play a pivotal role in the production of injection mold tools. They are responsible for precision machining and finishing of molds, which directly affects the quality of the finished products. At deepmould.net, our expertise in metal fabrication enables us to create high-precision molds tailored to the unique needs of our clients.
Types of Metal Fabrication Techniques Used in Injection Molding
Metal fabrication techniques for injection mold tools include:
- Machining: Involves removing material from a workpiece to create the desired shape and dimensions.
- Welding: Used to join different metal parts of the mold, ensuring robustness and durability.
- Grinding: Refines the surface finish of the mold, essential for achieving the desired quality of molded parts.
The Future of Injection Mold Tools
The landscape of injection mold tools is evolving with advancements in technology. Innovations such as 3D printing, CNC machining, and smart manufacturing are paving the way for more efficient and adaptable manufacturing processes. Additionally, there’s a growing emphasis on sustainability, with manufacturers seeking to minimize their environmental impact through eco-friendly materials and practices.
1. 3D Printing in Mold Design
3D printing is revolutionizing the design process for molds, enabling rapid prototyping and customization without the traditional lead times. This technology allows for testing designs quickly, reducing time-to-market for new products.
2. Smart Manufacturing
Integrating IoT technologies into the manufacturing process will enhance the monitoring and maintenance of injection mold tools, improving uptime and production quality.
Conclusion
In summary, injection mold tools are fundamental components of modern manufacturing, offering a blend of precision, efficiency, and versatility. The choice of the right tools can significantly impact the quality of the final products and the overall production costs. As the industry evolves, the integration of new technologies and techniques will continue to enhance the capabilities of injection molding. By partnering with skilled metal fabricators like those at deepmould.net, companies can ensure that they are equipped with the best tools available to meet the demands of their markets.
For more insights into injection mold tools and metal fabrication, visit deepmould.net today!