Custom Plastic Industrial Blade: Revolutionizing Industries
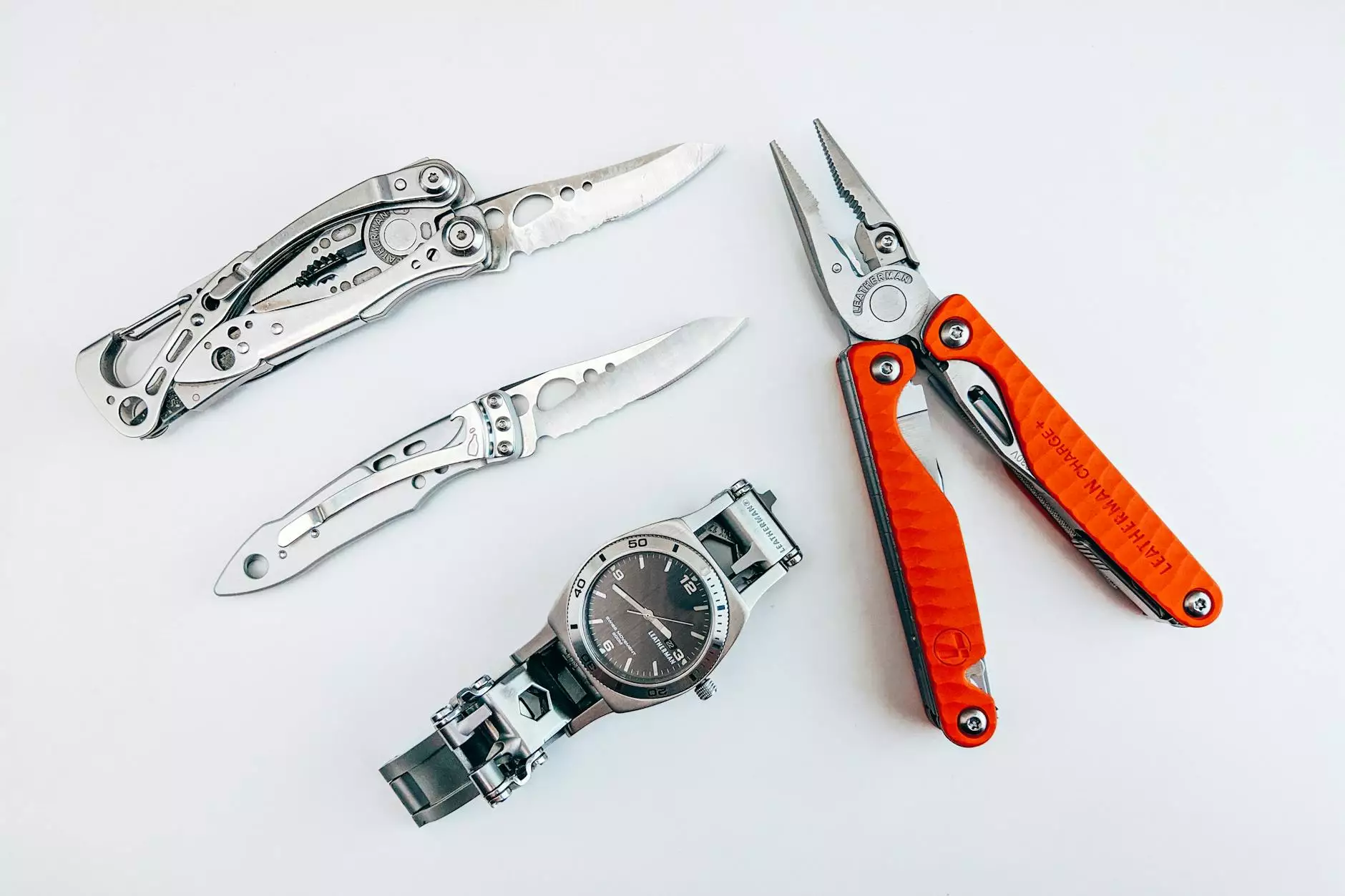
The world of manufacturing and industrial applications is continually evolving, driven by the need for efficiency, precision, and innovation. One area that has seen significant advancements is the development and usage of the custom plastic industrial blade. These specialized blades are crafted to meet the unique requirements of various industries, providing tailored solutions that enhance productivity and reduce costs.
Understanding Custom Plastic Industrial Blades
Custom plastic industrial blades are precision-engineered cutting tools designed specifically for industrial applications. Unlike standard blades, these custom solutions are made from high-quality plastic materials, which offer several advantages over traditional metal blades. They are lightweight, resistant to corrosion, and capable of cutting through a variety of materials with ease.
The Composition of Custom Plastic Blades
The materials used in the manufacturing of custom plastic blades include:
- Polyethylene (PE): Known for its durability and flexibility.
- Polypropylene (PP): Offers excellent chemical resistance and is lightweight.
- Polyvinyl Chloride (PVC): Ideal for applications requiring rigidity.
- Polycarbonate: Known for its clarity and impact resistance.
These materials are selected based on the specific application of the blade, ensuring optimal performance and longevity.
Applications of Custom Plastic Industrial Blades
The versatility of custom plastic industrial blades allows them to be utilized across a wide range of industries, including:
1. Food Processing Industry
In the food processing sector, hygiene and safety are paramount. Custom plastic blades are ideal due to their ease of cleaning and resistance to corrosion. They are often employed in:
- Chopping and slicing machines.
- Packaging equipment.
- Conveyor systems for food items.
2. Packaging Industry
Custom plastic blades play a crucial role in the packaging industry, where precision cutting is essential. Their lightweight nature reduces wear on machines, enhancing operational efficiency. Common applications include:
- Cutting film and plastic wraps.
- Trimming boxes and containers.
- Sealing processes.
3. Textile and Fabrication Sectors
In the textile industry, custom plastic blades are used to cut through various fabric types without fraying the edges. This ensures a clean finish, which is vital for quality control. Applications include:
- Cutting woven and non-woven fabrics.
- Slicing foam and padding materials.
- Precision cutting for complex designs.
Advantages of Using Custom Plastic Industrial Blades
The benefits of utilizing custom plastic industrial blades are numerous. Here are some of the key advantages:
1. Enhanced Performance
Custom blades are designed for specific tasks, which means they perform better than standard options. Users can expect:
- Increased efficiency in cutting operations.
- Reduced operational downtime due to fewer equipment failures.
2. Cost-Effective Solutions
Investing in specialized blades can lead to significant cost savings in the long run. Custom plastic blades often have:
- A lower initial cost compared to metal blades.
- A longer lifespan due to resistance to wear and tear.
3. Safety Features
The lightweight nature and material properties of plastic blades contribute to enhanced safety in the workplace. They are less likely to shatter and cause injury than their metal counterparts, making them a preferred choice for many organizations.
Customization Process of Plastic Industrial Blades
The process of creating custom plastic industrial blades involves several key steps to ensure that the final product meets precise specifications:
1. Initial Consultation
The process begins with a thorough consultation with the client. This involves discussing:
- The specific requirements of the blade.
- The materials to be cut.
- Operating conditions and environmental factors.
2. Design and Prototyping
Once the requirements are established, engineers create a design for the blade. This phase involves:
- Using CAD software to create a 3D model.
- Testing the design for functionality and performance.
3. Manufacturing
After finalizing the design, the manufacturing process begins. Modern techniques, such as:
- Injection molding.
- 3D printing.
- CNC machining.
are often employed to ensure precision and efficiency in production.
4. Quality Control
Before the blades are dispatched, a rigorous quality control process is undertaken to ensure that each blade meets the specified standards and performance metrics.
Choosing the Right Manufacturer for Custom Plastic Industrial Blades
When selecting a manufacturer for custom plastic industrial blades, it’s essential to consider several factors to ensure quality and reliability:
1. Experience and Expertise
Look for a manufacturer with a proven track record in producing industrial blades. Experience often correlates with the ability to deliver high-quality products tailored to your specific needs.
2. Innovation and Technology
Choose a manufacturer that employs advanced technologies and innovative materials in their production processes, as this can significantly impact the blade’s performance and durability.
3. Customer Support
A great manufacturer will offer comprehensive customer support, including assistance before, during, and after the purchase. This ensures any questions or concerns are promptly addressed.
Conclusion
The importance of custom plastic industrial blades in modern industrial applications cannot be overstated. Their tailor-made design, coupled with the benefits of lightweight and corrosion-resistant materials, positions them as essential tools across a variety of sectors. By investing in custom solutions, businesses can enhance their operational efficiency, cut costs, and ultimately improve their bottom line. To find the right solution for your needs, consider reaching out to industry leaders such as szblade.com, who specialize in professional services including knife sharpening and custom blade manufacturing.